What is a Warehouse Management System?
A warehouse management system (WMS) is a piece of software which automates key warehouse processes. A WMS uses barcodes and radio frequency (RF) handheld terminals and other mobile devices to direct and track the movements of products and people within the warehouse, providing a real-time picture of all activities.
The system also generates all the tasks which must be performed at each stage in the warehouse process. These instructions are delivered to staff and confirmed back to the system via the handheld terminals. Every warehouse is unique and comes with its own challenges. A flexible, real-time WMS can cater to almost any scenario.
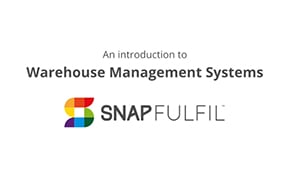
Read on to view the processes a best-of-breed warehouse management system covers and watch a full video of how it works here: An Introduction to Warehouse Management Systems.
Goods-in / Receiving
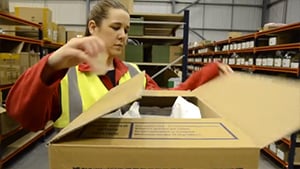
When receiving products, paper lists, such as delivery notes, are commonly used to reconcile actual deliveries with expected receipts. With a warehouse management system, operators inspect and record receipts on a mobile handheld terminal, scanning barcodes where available to enhance accuracy. The WMS then automatically reconciles these against purchase order information in the system and either confirms that the delivery is correct or flags any discrepancies.
If you have multiple purchase orders with the same supplier, the system can create a consignment that allows operators to receive against all purchase orders (typically the oldest first) and streamline the goods-in process without losing traceability.
Put-away
Put-away falls into two core types - either putting away pallet to bulk storage or smaller amounts of individual SKUs into picking locations. Many warehouses need their goods to be picked from anywhere, while larger operations may use bulk storage and specified pick faces. A warehouse management system can enhance both of these put-away setups. A series of simple and easy to follow instructions are issued to warehouse staff via the handheld device. This requires little to no training to use and reduces the chance that operators will make a mistake.
In addition to managing your inventory, a warehouse management system will also control and allocate your resources in the most efficient way. As soon as a task is completed, the system will look for the next priority task that an operator is authorized to do and will assign it to them automatically.
Inventory
When it comes to inventory management, warehouses have little room for error. The inventory function is where all of the products handled by the warehouse are defined to the system. These product attributes are then used by the warehouse management system's rules engine to drive the agreed operational processes, for everything from receiving and putting away to storage location (for example, no liquids stored over solids), and finally, to picking and dispatch criteria.
One of the most useful features of a WMS is pick-face replenishment. It can be frustrating for pickers if the stock isn't in the right place at the right time. A real-time task management system will detect that a location has reached an agreed minimum and create a task to top up the location and will make this task a priority if an order is waiting. You can also interrogate the warehouse management system to show you stock information at a summary level and in detail.
Picking
Order fulfillment comes in all shapes and sizes, from full pallet picking through to case and item picking, from a wide variety of locations. A best-of-breed WMS will cater for all of these within a single operation if required. A key efficiency gain is the ability to pick more than one order in a single walk, or even better, the ability to use an autonomous mobile robot (AMR) for more advanced and efficient cellular picking.
A real-time system will also take into account next-day orders so these can automatically be assigned to a pick walk as soon as they are received. Each picking routine will be carefully designed to cater for the smallest, largest, and average order size required by your operation, ensuring the optimal pick sequence and path for every order or batch of orders.
Packing
Depending on your specific business, the relative order size and the amount of items that are barcoded will affect how orders are packed. In the example of an e-commerce company, orders are scanned to verify accuracy and that the correct dispatch box is selected. Labels and dispatch notes are automatically generated and can be configured to meet your specific requirements.
Most warehouse management systems integrate directly with a range of parcel carriers, such as FedEx and USPS, and also carrier management systems, such as RateLinx or Shippo. These integrations will not only generate the correct labels for each carrier and service type, but will also automatically generate export paperwork and end-of-the-day files where required. Some warehouse management systems also support the same process, but in reverse, for the effective management of returned items.
Reporting
Quickly identifying problem orders, locations, or inefficient operatives could save you time and money. Advanced warehouse management systems can provide an at-a-glance picture of warehouse performance against key performance indicators, supporting data-driven decision making in real time. Some also provide access to historical data, allowing you to accurately forecast resourcing requirements, monitor performance over time, and identify areas for improvement.
Warehouse management systems with more powerful reporting capabilities can also manipulate and blend stored information and client data across various sources into one cloud-based central dashboard. This gives your business the ability to make the best decisions from an amalgamation of key metrics.
Why Do I Need a WMS?
A warehouse management system can help your business become significantly more efficient in warehouse operations. Even if your business is already operating with great efficiency, you would be surprised at how much of an improvement you would see with a WMS in place. Here at SnapFulfil, our customers receive up to a 30% increase in productivity and warehouse efficiency.
If you're experiencing any of the challenges listed below, it is likely time for your company to look into implementing a warehouse management system, whether that be for the first time or replacing an outdated/legacy solution.
- Rapid growth
- Overwhelmed by high order volumes
- Inventory management is unreliable, causing you to reorder too much or too little product
- Conducting inventory on spreadsheets or paper
- High labor or inventory costs that damage profit margins
- Difficulty meeting peak seasonal demands
- New facilities or acquisitions
- Falling behind the competition
- Inability to adapt to new customer shipping expectations like two day shipping or international delivery
- Poor visibility of the entire order fulfillment cycle
- Costly shipping errors
- Warehouse workers are losing productivity
- Processing returns is inefficient
While this list is not exhaustive, it does cover some of the more common warehousing pain points. If you are experiencing at least a couple of these, it's a good time to start looking at warehouse management systems.
For large, enterprise-level companies you may have these processes down very well in your main distribution center (DC). But your regional DCs may be lagging behind or experiencing some of the challenges listed above. In that case, it is a good idea to start investigating the idea of a two-tiered WMS system (often referred to as Industry 4.0). A two-tiered system allows you to maintain your current WMS at the main DC and implement a versatile and adaptable cloud WMS at your regional DCs which can easily and seamlessly integrate with your main DC's warehouse system. Here at SnapFulfil we are seeing several of our larger customers improve their overall productivity with this approach.
Warehouse Management White Papers
If you'd like more detailed information about warehouse management systems you can learn more in these related white papers below. And for even more content you can browse our full collection of Resources here.
4 Signs It's Time For a New WMS
Successfully managing the logistics operations of a growing e-commerce business is no easy task, no matter how you're going about it. However, in the rush to fulfill orders, refund returns and keep shelves stocked, you may be falling behind your true potential.
Many businesses use a warehouse management system to keep track of orders and stay on top of inventory planning, among many other essential logistics tasks. The WMS may take the form of an on-premises software solution or perhaps even a large spreadsheet or even a paper filing system developed through trial and error. While these methods may get the job done, it can be hard to realize the efficiency and control you could be missing out on by neglecting to update this key part of your supply chain.
Whether you're just getting by or are already considering making a switch, here are a few key signs that it's time to upgrade to the next generation of warehouse management systems:
- Business is Booming
- Accepting the Status Quo for Too Long
- Still Using Spreadsheets
- Going Global
Building the Business Case for WMS
Properly understanding when, how and to what extent a warehouse management system will contribute to process efficiencies and costs savings is key to making the right decision for your business. There are four steps involved in establishing credit ROI calculations and estimates to build your case for a new WMS.
- Collect and understand all current costs
- Articulate a value statement for each cost compound
- Understand your processes
- Accept help from your vendor, but perform calculations independently
Knowing When to Invest in New Warehouse Software
Investing in a warehouse management system (WMS) is a big decision: defining requirements, evaluating vendors, negotiating terms, implementation and stabilization are all discrete and complex activities. they take time and are usually performed in addition to other responsibilities. So, when does it make sense to go through that effort?
There are three aspects of your company and warehouse's growth that should pique your interest in improving your current WMS technology:
- Strategic Plans
- Compelling Events
- Warehouse Operations
Three Hacks For a Successful WMS Implementation
You've selected a vendor, agreed on pricing and timing, and now you're getting ready to kick off one of the most disruptive, risky and complex tasks in a warehouse. Sounds fun, right? Not really - but there are a few practices that, even if you've never implemented a new warehouse management system before, will increase the likelihood of success:
- Prepare your organization.
- Stay aligned with your vendor.
- Remove obstacles.
Download the white paper for more details.